Agentic AI for Power Transformer Fleet Management
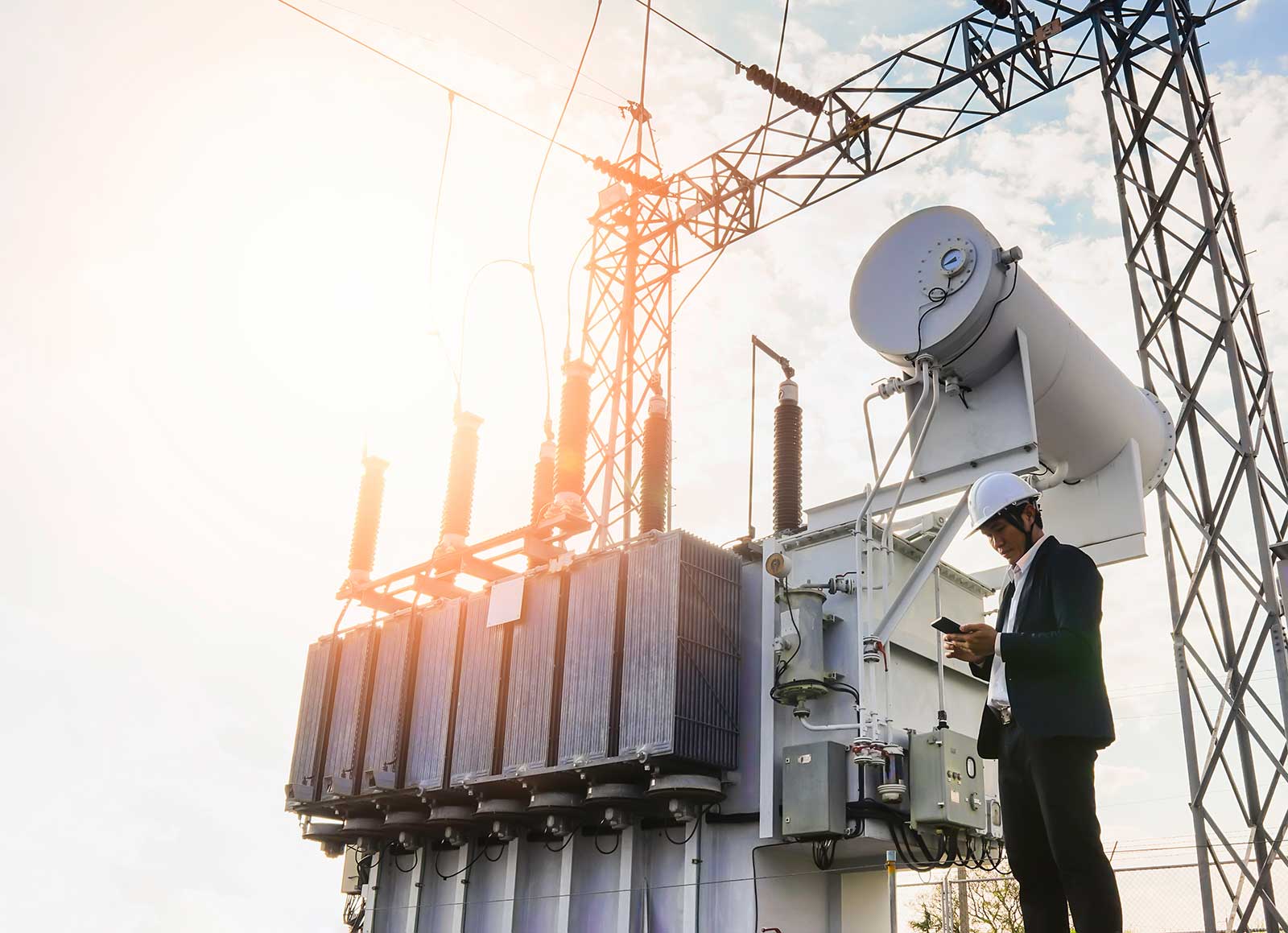
Agentic AI powers condition-based transformer maintenance with DGA/PD monitoring & SCADA integration, reducing failures and meeting NERC, IEC & CIGRE standards.
Table of Contents
- Agentic AI and Transformer Maintenance: The PowerGrids AI Case Study
- The Need for Condition-Based Maintenance
- Transformer Condition Monitoring Techniques
- Agentic AI Meets Transformer Fleet Management
- PowerGrids AI Platform: Key Capabilities
- Competitive Comparison
- Impact on Reliability and Performance
- Future Outlook and Analyst Perspectives
- Frequently Asked Questions
Agentic AI and Transformer Maintenance: The PowerGrids AI Case Study
PowerGrid operators face a critical challenge: aging transformer fleets coupled with intermittent monitoring lead to costly, unplanned failures. Traditional calendar-based maintenance often misses hidden faults, whereas Condition-Based Maintenance (CBM) can catch issues early. This case study examines how an agentic AI platform – embodied by PowerGrids AI – transforms transformer maintenance by integrating real-time monitoring (e.g. DGA, partial discharge) with advanced analytics. We compare PowerGrids AI’s capabilities to IPS Transformer Intelligence Center, GE Vernova APM Health, and Hitachi APM Edge, highlighting how PowerGrids AI’s autonomous, data-driven approach can significantly reduce failure rates and improve grid reliability. Emphasis is placed on scholarly research (IEEE, IEC, CIGRÉ, and leading industry sources) and standards to substantiate the analysis.
Figure: Example transformer substation. Modern CBM uses online monitoring (sensors on units like this) and analytics to detect incipient faults early.
The Need for Condition-Based Maintenance
The electric grid’s reliability hinges on power transformers. A single large transformer failure can interrupt supply to hundreds of thousands of customers and incur millions in costs. Yet, many time-based maintenance schedules fail to prevent such events. Studies show transformer failure rates are roughly constant over much of a unit’s life (a “flat hazard rate” in mid-life), meaning many failures occur unpredictably rather than on a set schedule. In practice, a transformer might pass an inspection and then fail weeks later without warning. As CIGRE notes, “time since last maintenance has weak correlation with many failure modes, underlining the need for continuous condition tracking”.
Conversely, conditioning monitoring (CBM) can be cost-effective. Instead of routine overhauls on all units, CBM uses sensor data to service transformers only when needed, avoiding unnecessary work and downtime. For example, continuous Dissolved Gas Analysis (DGA) can flag insulation faults, and Partial Discharge (PD) detectors can warn of winding defects, long before catastrophic failure. Research and field experience demonstrate CBM extends asset life and cuts outages by catching problems early. Utilities and regulators agree: asset management focus is shifting from calendars to condition-based, risk-informed strategies.
Key industry bodies advocate this change. CIGRE’s Technical Brochure (WG A2.49) outlines how to combine diagnostic data into health indices and risk scores, enabling prioritization of critical units. Likewise, North American reliability organizations (e.g. NERC) emphasize improved asset management to avoid failures. Indeed, CIGRE finds that utilities implementing modern monitoring (online DGA, PD, etc.) achieve far lower failure rates (~0.1–0.2% per year), roughly one-fifth of older fleets. These declines are credited to better diagnostics and proactive maintenance.
In summary, CBM shifts the paradigm: maintenance tasks (oil tests, inspections, repairs) occur as-needed based on equipment condition, rather than on a fixed timetable. This maximizes reliability and asset utilization while minimizing unnecessary outages and costs.
Transformer Condition Monitoring Techniques
Modern CBM relies on multiple diagnostics. Dissolved Gas Analysis (DGA) – often called the “blood test” for transformers – examines gases dissolved in the insulating oil. When insulation or copper is stressed (thermal faults, arcing, partial discharge), characteristic gases form and dissolve in oil. Analyzing these gases can identify fault type and severity. As GE notes, “DGA has long been recognized as the single most powerful technique for transformer main tank fault detection/prediction”. By contrast to a simple threshold, modern CBM systems trend gas concentrations over time and use statistical/failure data to interpret subtle changes.
Other key monitoring methods include Partial Discharge (PD) detection, thermal and oil-flow sensors, and electrical tests. PD sensors detect high-frequency pulses from insulation defects. Thermal monitoring (temperature and load sensors) tracks hotspots. Standard tests like Sweep-Frequency Response Analysis (SFRA) and insulation power-factor tests, though often done offline, reveal mechanical or dielectric issues in windings. Each of these methods provides a piece of the condition picture. In practice, utilities collect both real-time and historical data: for example, field sensors stream DGA and PD, while laboratory oil tests and periodic SFRA results feed into the assessment.
Importantly, multiple data sources are most informative when analyzed together. CIGRE’s methodology recommends combining DGA results with other parameters (load, ambient conditions, past repairs) into a unified health index. If, for instance, oil tests show rising acetylene levels (indicative of arcing) while PD detectors report activity, the likelihood of failure is high; conversely, isolated gas spikes might be benign if cooling was briefly impeded. CBM systems thus fuse electrical, chemical, and operational data to estimate asset health continuously.
Figure: Categories of transformer monitoring parameters and diagnostics (e.g. DGA for gas faults, PD for insulation, thermal sensors for overheating), as outlined in CIGRÉ and academic studies.
Agentic AI Meets Transformer Fleet Management
Advances in Artificial Intelligence (AI) now enable truly autonomous CBM. Agentic AI refers to systems that can perceive data, make decisions, and act with minimal human oversight. In the context of transformers, an agentic AI “platform” continuously ingests sensor streams (SCADA feed, DGA monitors, PD detectors) along with historical records (past oil samples, maintenance logs, nameplate parameters). It then applies machine learning and expert algorithms to compute each asset’s health and predict failures. Crucially, unlike rule-based alerts, an agentic system can autonomously trigger actions: for example, creating maintenance work orders or issuing executive risk reports without waiting for a human to analyze data.
The PowerGrids AI platform exemplifies this approach. It integrates with existing utility systems – SCADA (for real-time load/temperature), APM/EAM databases, GIS maps, etc. – and continuously monitors every transformer via online DGA, PD sensors, temperature sensors and more. The agentic AI agents operate like “24/7 digital guardians” for each unit: they detect abnormal patterns, assess failure risk, and can recommend or even initiate maintenance workflows directly. For instance, if the AI sees a sudden jump in acetylene and a high PD count on Transformer T1, it might automatically generate a DGA lab test and tap-changer inspection work order in the maintenance system.
This fully integrated CBM loop is key. By fetching nameplate data (e.g. MVA rating, voltage class, OLTC type) and history from APM records, the AI contextualizes sensor anomalies. For example, if a transformer had new bushings installed recently, an AI alarm on a bushing sensor could be flagged as likely sensor error. After maintenance actions occur, the AI also ingests the results (e.g. “insulation power factor improved”) to update its models. Over time, its health indices and risk scores are refined. As CIGRE notes, combining all available data into health indices enables truly risk-based maintenance prioritization.
PowerGrids AI’s agentic architecture thus not only senses but acts. Preliminary industry reports indicate this can drive failure rates down: a 2024 CIGRE survey found failure rates ~0.1–0.2%/year in fleets using modern monitoring and CBM. Agentic AI could push this further by making the maintenance process continuous and proactive rather than reactive. For utilities, the promise is clear: fewer outages, more efficient maintenance budgets, and data-backed confidence in decision-making.
PowerGrids AI Platform: Key Capabilities
Integrated Data Ingestion: Interfaces with SCADA, GIS, APM/EAM databases and document repositories. It ingests real-time sensor data (online DGA monitors, PD detectors, temperature and bushing monitors) alongside historical records (laboratory DGA results, previous electrical test logs, maintenance notes, nameplate specs). This holistic data fusion is beyond many legacy systems.
Proprietary Machine Learning: The agentic AI is trained on thousands of transformer oil data sets and operational scenarios (from global fleets). It uses both unsupervised anomaly detection and supervised models (e.g. random forests, neural nets) to classify fault conditions. For example, while IEC and IEEE provide DGA interpretation guides (e.g. IEEE C57.104, IEC 60599), the AI refines these with real-world failure statistics. The result is more nuanced diagnostics and earlier warnings.
Autonomous Decision-Making: Instead of static alerts, the agents generate actionable outcomes. This includes auto-creating work orders in the utility’s APM/EAM system. The system can prioritize issues based on fleet-wide risk scoring. Executives can view dashboard reports that stratify the fleet into “critical”, “poor”, “fair”, and “good” health categories – a capability envisioned by CIGRE’s condition assessment methodology.
Transformer Benchmarking: PowerGrids AI uniquely processes nameplate data and manufacturer manuals (Siemens, GE, Hitachi, etc.) to benchmark each transformer against similar units. For example, two 200 MVA, 115/12 kV OLTC transformers with similar age and duty can be compared in terms of oil aging or PD patterns. This feature uses AI to parse specification sheets and compare across a fleet. Such “apples-to-apples” benchmarkinghelps validate whether a given gas rise is unusually high or normal for that design – a task beyond standard APM tools.
CIGRE/IEC Compliance: The platform embeds standards. It considers IEC 60076 guidance on moisture and thermal limits, CIGRE TB 761 indices for failure probability, and IEEE Std C57.143 recommendations for integrating monitoring into asset management. By aligning with these best practices, PowerGrids AI ensures its maintenance policies meet regulatory and industry frameworks.
Competitive Comparison
IPS Transformer Intelligence Center (TIC): IPS’s solution centralizes transformer oil test data and uses machine learning diagnostics. It boasts a vast oil test database (leveraging Megger’s lab results) and provides predictive insights for maintenance planning. Key features include automated oil test data management, specialized diagnostics (e.g. Chemical Physical Assessment), and fleet health summaries. Like PowerGrids, IPS uses ML on oil chemistry, but it is primarily lab-based: it focuses on offline DGA and CPA results. It improves decision-making with fleet risk reports, but does not claim fully autonomous action – planners typically review IPS-TIC alerts to schedule work. There is no mention of parsing transformer manuals or real-time sensor integration in IPS’s materials. In short, IPS TIC excels at analytics on extensive oil-test histories, whereas PowerGrids AI adds continuous sensor data and an agentic execution layer.
GE Vernova APM (APM Health): GE’s APM Health is a broad asset management module (part of Proficy software) for many asset types, including transformers. It unifies diverse asset data (OT/IT, alarms, manual rounds) to give operators near-real-time visibility of health. Key features include mobile-enabled operator rounds, dashboards for condition visibility, and integration with maintenance workflows. GE touts its Verdantix leadership ratings and “perfect score” for APM Health’s condition monitoring capabilities. However, GE’s platform is less specialized on transformer physics. It provides infrastructure (data collection, visualization, work-order generation) but relies on user-defined rules or third-party analytics for actual fault detection. Unlike PowerGrids, GE’s APM does not claim proprietary transformer algorithms or autonomous agents. It does incorporate AI/analytics (e.g. integration with GE Digital’s SmartSignal), but these are general and need significant configuration.
Hitachi Energy APM Edge (Lumada): Hitachi APM Edge is a turnkey solution for transformer asset management, leveraging the Lumada APM platform and Hitachi’s TXpert™ sensors. TXpert monitors (onboard transformers) provide online DGA, bushing, and temperature data. The APM Edge integrates these sensor feeds to offer actionable insights (e.g. “minimize downtime by ranking units by risk”). Hitachi emphasizes ease of deployment and scalability (from single units to enterprise-wide). It helps utilities transition to CBM by combining sensor data with Hitachi’s grid expertise. In effect, it is somewhat similar to PowerGrids AI in targeting transformer health. The distinction is that Hitachi’s platform is a packaged OEM solution (with proprietary sensors and support), whereas PowerGrids AI is an asset-agnostic software layer that can integrate any manufacturer’s sensors and data. Additionally, Hitachi’s offering still positions humans in the loop for decision-making; it does not claim fully autonomous AI agents.
The table below summarizes how these solutions compare on key transformer-maintenance features:
Capability | PowerGrids AI (Agentic APM) | IPS Transformer Intelligence (TIC) | GE Vernova APM Health | Hitachi APM Edge (Lumada) |
---|---|---|---|---|
Data Sources | Online DGA and PD sensors; historical lab DGA & electrical tests; GIS, SCADA integration | Laboratory oil test results; transformer electrical test data | Any operational/IT data; supports manual rounds and SCADA data | Online TXpert sensor data (DGA, bushings, temp); GIS/SCADA inputs |
AI/ML Analytics | Proprietary ML on thousands of global oil & sensor datasets; agentic decision-making | ML diagnostics on oil chemistry (Chemical Physical Assessment) | Predictive analytics available (e.g. SmartSignal), but typically requires engineering setup | Embedded analytics from sensors; Lumada platform uses AI tools |
Autonomy | Fully autonomous AI agents that generate alerts/work orders | Alerts based on ML scoring; manual review typically required | Generates real-time dashboards and alerts; technician executes actions | Provides recommendations; user schedules/executes maintenance |
Transformer Benchmarking | Compares any unit to peer fleet based on nameplate and operational data (via AI parsing of manuals) | Fleet comparison on oil test trends; limited to database values | No built-in transformer benchmarking (generalist platform) | Compares monitored data to typical thresholds; limited benchmarking |
Health Indices & Risk | Computes health index and failure probability continuously (fleet ranking) | Offers risk scores from oil analysis; fleet summary reports | Provides asset condition scores from combined data | Generates health dashboard; risk assessment via sensor insights |
Integration (APM/EAM) | Deep SCADA/GIS/APM integration; auto-creates work orders | Focused on transformer data; can feed results to planners | Tight integration with GE’s EAM/SCADA; supports GIS & mobile | Integrates with Hitachi WFM/EAM; geared to Hitachi ecosystem |
Deployment Scope | Vendor-neutral software (cloud/on-prem); scalable from single fleet to enterprise | Primarily fleet maintenance tool; offered as SaaS | Enterprise APM suite for all industries/assets | Solution for electrical utilities; requires Hitachi sensors |
Each solution improves on traditional maintenance in different ways. IPS TIC and Hitachi APM bring proven transformer-domain expertise, while GE and Hitachi leverage broad APM platforms. PowerGrids AI distinguishes itself by combining all these: transformer-specific intelligence plus an autonomous AI layer that ties directly into maintenance workflows.
Impact on Reliability and Performance
Case studies and surveys indicate that advanced CBM yields tangible results. Utilities using modern monitoring report dramatically lower failure rates. For example, fleets with aggressive online monitoring have seen failure rates around 0.1–0.2% per year. A Bain report describes a North American utility that, by adding transformer load profiles and outage history into analytics, improved its failure prediction accuracy 3–4× over traditional age-based models. This kind of predictive edge lets executives plan replacements or overhauls only when needed, rather than on fixed schedules.
By enabling predictive interventions, agentic AI can further boost these gains. For instance, if PowerGrids AI flags an impending bushing failure from gas trends and PD spikes, maintenance can be scheduled during planned outages, avoiding unplanned downtime. Studies show that targeted maintenance (CBM) can reduce unplanned outages by over 30–50% in mature systems. Meanwhile, asset life is extended by avoiding unnecessary disassembly of healthy transformers (as occurs in rigid time-based programs).
Beyond outages, AI-driven CBM improves maintenance efficiency. Work crews are directed by data, focusing on the riskiest assets. PowerGrids AI’s integrated platform can, for example, rank a fleet of 100 transformers by risk: perhaps 5 “critical” needing replacement, 20 “poor” needing near-term repair, while 50 are “fair” (monitor only) and 25 are “good”. This level of insight – automatable via AI – helps utilities allocate budgets optimally. As CIGRE notes, maintenance prioritization should be “based on reliable health indices” and performance metrics.
Finally, CBM generates a wealth of data for continuous improvement. Every oil sample and sensor reading feeds back into the system. Over time, utilities can refine their maintenance strategy (e.g. extending intervals for a quiet asset), a flexibility impossible with rigid schedules. With AI, each intervention itself becomes data: after a fault is fixed, the system learns to update its alarm thresholds. This closed-loop learning means the transformer fleet’s reliability improves year-over-year as the AI accrues experience.
Future Outlook and Analyst Perspectives
Looking ahead, agentic CBM platforms like PowerGrids AI could reshape the APM market. Gartner and industry analysts emphasize that asset performance solutions now revolve around AI, IoT, and digitalization. Verdantix’s 2024 Green Quadrant report observes that top APM vendors differentiate themselves by embracing “the latest advancements in AI and generative AI”, as well as support for environmental and reliability goals. PowerGrids AI fits neatly into this trend: its core is AI-driven analytics and it explicitly uses real-time IoT sensor data.
Although Gartner has not published a dedicated “Magic Quadrant for APM” as of mid-2025, Verdantix’s Green Quadrant highlights leaders like ABB, AVEVA, GE Vernova, Honeywell, IBM, etc.. These incumbents currently dominate by broad feature sets. PowerGrids AI’s focus on transformers and autonomous agents would likely position it as a visionary in future evaluations. Its novel capabilities (e.g. nameplate-based benchmarking, self-driving maintenance workflows) could give it momentum if customer references grow.
Indeed, Gartner-style quadrants reward completeness of vision and execution. PowerGrids AI’s innovation in AI and integration could align with these criteria. For instance, Verdantix notes industry momentum favors scalable, cloud-based APM with AI enhancements. By demonstrating operational impact (failure reduction, cost savings), PowerGrids AI could argue for leadership placement in time. Additionally, as sustainability and Net-Zero agendas press utilities, CBM platforms that maximize asset utilization also support environmental goals. Offering compliance with standards (IEC 60076, IEEE, CIGRE guidelines) further strengthens its enterprise case.
In summary, PowerGrids AI’s strategic positioning is promising: it addresses a high-value pain point (transformer reliability) with cutting-edge technology. If it can capture meaningful market share and endorsements, analysts may soon recognize it as a leader in next-generation APM.
Frequently Asked Questions
What is Condition-Based Maintenance (CBM)? CBM means servicing equipment based on its actual health data rather than a fixed schedule. For transformers, this involves continuous monitoring of key parameters (gas in oil, partial discharge, temperature, etc.) and doing maintenance “as-needed” to prevent failures. By acting on data trends, CBM can prevent unexpected outages and extend asset life.
How does CBM differ from preventive or corrective maintenance? Preventive maintenance is time-based (e.g. overhauls every 5 years). Corrective maintenance is run-to-failure. CBM is a middle ground: it uses real-time condition data to predict and prevent failures. Unlike preventive (which can be wasteful) or corrective (which risks unplanned outages), CBM optimizes interventions for actual asset needs.
What is Dissolved Gas Analysis (DGA)? DGA is a diagnostic technique for oil-filled transformers. When internal faults occur (arcing, overheating, partial discharge), gases form in the oil. DGA measures the concentrations of gases like hydrogen, acetylene, methane, etc. in oil samples. The gas signature reveals fault type and severity. It is widely regarded as the most powerful single tool for detecting impending transformer failures.
What is Partial Discharge (PD) monitoring? PD monitoring detects localized electrical discharges (sparks) within transformer insulation. PD pulses generate high-frequency signals that can be measured externally. Persistent PD indicates insulation degradation. Continuous PD monitors provide early warning of developing defects that might not yet show in oil tests. In combination with DGA, PD greatly improves fault detection sensitivity.
What is an Asset Performance Management (APM) platform? APM software brings together asset data (sensors, inspections, maintenance records) to improve reliability and efficiency. It typically includes dashboards, analytics, and maintenance planning tools. Modern APM solutions (like GE’s APM Health or Hitachi Lumada) often integrate IoT data and analytics to support CBM. PowerGrids AI is an advanced form of APM focused on transformers, adding autonomous decision-making (agentic AI) on top of standard APM features.
What makes PowerGrids AI’s approach unique? PowerGrids AI distinguishes itself by combining agentic AI (autonomous analytics agents) with both real-time and historical data across systems. Unlike traditional APM, it automatically reasons with transformer-specific knowledge. It not only predicts faults (from DGA and PD), but can parse transformer nameplates/manuals, benchmark units against peers, and even create maintenance work orders autonomously. This end-to-end automation – from sensor to decision – is what “agentic” AI brings to CBM.
How are transformer nameplates and manuals used? PowerGrids AI can ingest static details (e.g. MVA rating, voltages, tap-changer type, oil volume) from nameplate data and manufacturer specs. These details help the AI tailor its analysis – for example, understanding a transformer’s design limits or cooling method. By comparing two similar units’ specifications, the AI can benchmark performance. (For instance, a 50 °C rise might be normal for one design but alarming for another.) This semantic understanding of transformer designs is a novel capability.
What standards and guidelines support CBM? Many IEC and CIGRÉ standards endorse CBM concepts. For example, IEC 60599 and IEEE C57.104 provide DGA interpretation guides; IEC 60076 series covers transformer insulation tests; CIGRÉ TB 761 details condition indices and risk-based maintenance. PowerGrids AI is built to comply with these standards, ensuring its recommendations align with best practices (e.g. factoring in humidity or gas trends as IEEE/IEC recommend).
How does CBM reduce power failure rates? By detecting faults early, CBM prevents unexpected trips. Studies show most transformer outages are due to known issues (bushings, cooling, OLTC) that can be monitored. With continuous data and AI analytics, utilities can catch issues weeks or months in advance. The 2024 CIGRE survey noted very low failure rates in fleets using advanced monitoring. Quantitatively, typical outages per transformer per year can drop from ~0.5% (or higher in old fleets) to well under 0.2% with CBM.
What role does AI play in CBM? AI (especially machine learning) excels at finding patterns in large sensor datasets. It can improve on traditional rule-based thresholds by learning from history. In practical terms, AI can correlate multi-dimensional signals (gas, temperature, load) faster and more accurately than human engineers. Generative AI (GenAI) is even being used for things like reading maintenance reports or vendor manuals to extract knowledge. PowerGrids AI leverages these to continuously refine its diagnostics and suggest optimal actions.
How do these solutions compare on features? (See the table above.) In brief, IPS TIC focuses on extensive oil-test analytics; GE APM is a general platform providing data unification and operator workflows; Hitachi APM Edge integrates transformer sensors with a packaged APM solution. PowerGrids AI adds an autonomous agentic layer and deep transformer-domain intelligence. Each has strengths, but PowerGrids AI’s combination of real-time sensors, historical analysis, and self-driving maintenance makes it a disruptive entrant in the APM space.
Sources: IEEE standards (e.g. C57.104), CIGRÉ reports (e.g. TB761), and industry whitepapers are cited above to substantiate transformer CBM methods.
Share this article: